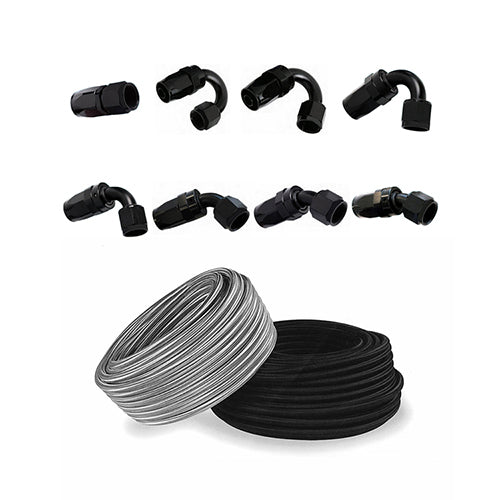
AN Fitting Size Chart & A History of AN Sizing
When it comes to automotive plumbing, AN Fittings and Flexible AN Hose have become the go-to choice for high-performance fluid control applications. However, understanding the sizing conventions of AN fittings can be confusing, with multiple different systems used. We hope that the table provided below, along with a brief history of AN sizing, will be useful.
Below is a table displaying AN sizes from -3AN to -20AN, the corresponding SAE thread size, and matching tube size:
AN Size | SAE Thread Size | Tube Size (inches) |
---|---|---|
-3AN | 3/8"-24 | 3/16" |
-4AN | 7/16"-20 | 1/4" |
-6AN | 9/16"-18 | 3/8" |
-8AN | 3/4"-16 | 1/2" |
-10AN | 7/8"-14 | 5/8" |
-12AN | 1 1/16"-12 | 3/4" |
-16AN | 1 5/16"-12 | 1" |
-20AN | 1 5/8"-12 | 1 1/4" |
It's important to note that AN sizes are based on the outside diameter of the fitting, while the corresponding SAE thread size is based on the inside diameter of the fitting. This means that different AN sizes can have the same SAE thread size, and vice versa. Please note, AN sizes are not the same as NPT (National Pipe Thread) sizes, so it's important to use the correct fittings and adapters when working with AN fittings and hoses. Additionally, tube size refers to the outside diameter of the tube being used with the fitting. It's important to use the correct size of tube with AN fittings to ensure a proper seal and prevent leaks.
A BRIEF HISTORY OF AN SIZING
AN fittings and hoses are common in the automotive industry today, especially in high-performance and racing applications. They are known for their high-pressure capabilities, durability, and resistance to leakage, making them ideal for applications where safety and reliability are critical. But, where did the AN sizing system come from, and how did it become so popular in the automotive industry?
The AN sizing system originated in the aviation industry during World War II when the US Army and Navy needed standardized fittings and hoses for their aircraft. AN stands for "Army/Navy," and the system was developed to ensure that all fittings and hoses used in military aircraft were interchangeable, regardless of the manufacturer. The AN sizing system uses a combination of numbers and letters to designate the size of the fitting or hose. For example, AN-6 refers to a fitting or hose with a 6/16 inch (or 3/8 inch) diameter.
After the war, the AN sizing system was adopted by the racing industry, where it quickly became the standard for high-performance applications. Racers appreciated the AN system's reliability, consistency, and ease of use, and it quickly became the go-to system for fuel lines, oil lines, and other high-pressure applications. Today, AN fittings and hoses are used in a wide range of applications, from high-performance street cars to professional race cars.
AN fittings are available in a variety of materials, including aluminum, stainless steel, and brass. Aluminum fittings are the most common and are suitable for most applications. Stainless steel fittings are more durable and corrosion-resistant, making them ideal for use in harsh environments or with aggressive fluids. Brass fittings are less expensive than aluminum or stainless steel but are not as durable or corrosion-resistant.
AN hoses are typically made from synthetic rubber or PTFE (Polytetrafluoroethylene) and are available in various sizes and lengths. Synthetic rubber hoses are suitable for most applications and are more flexible and easier to work with than PTFE hoses. PTFE hoses are more expensive than synthetic rubber hoses but offer superior chemical resistance and can handle higher temperatures and pressures.
In summary, the AN sizing system was developed by the US Army and Navy during World War II to standardize fittings and hoses used in military aircraft. After the war, the system was adopted by the racing industry, where it quickly became the standard for high-performance applications. Today, AN fittings and hoses are widely used in the automotive industry, where their high-pressure capabilities, durability, and resistance to leakage make them ideal for applications where safety and reliability are critical.
Leave a comment